Anticipating the Hardening Response of Aluminium-bearing Plain-carbon Steels
Addressed the unexpectedly poor response (low hardness and/or case depth), of a steel containing significant levels of aluminium, after heat treatment under normal conditions which would otherwise be expected to yield satisfactory results.
ANTICIPATING THE HARDENING RESPONSE OF ALUMINIUM-BEARING PLAIN-CARBON STEELS
A previously-issued joint statement by the Steel Industry/Contract Heat Treatment Association working party drew attention to the heat-treatment response problems which can be encountered in the case-harden- ing (carburising / carbonitriding) or direct-hardening of components made from aluminium-bearing plain-carbon (and some low-alloy) steels. In view of the paucity of specific data identified therein, this technical note from the working party is intended to give broad guidance to those involved in steel selection and heat treatment.
A ROUGH BASIS FOR ASSESSMENT
The problem being addressed is the unexpectedly poor response (low hardness and/or case depth), of a steel containing significant levels of aluminium, after heat treatment under normal conditions which would otherwise be expected to yield satisfactory results.
The cause of the problem has been identified as the fine grain size (and thus reduced hardenability) developed in these steels at the highest (austenitisation) temperature to which they are heated prior to quenching. Because it is dictated by the amount, form and distribution of aluminium nitride precipitated in the steel, the grain size is not merely a function of aluminium content; it also depends strongly upon the nitrogen level in the steel and the austenitisation conditions.
The graph shown here, based upon the calculations of Gladman(8), illustrates how these factors together influence the development of fine or coarse grain size when austenitising at 925°C (typical carburising temperature used for low-carbon steels), 880°C (representative of carbonitriding temperatures) and 850°C (relevant to the hardening of medium-carbon steels).
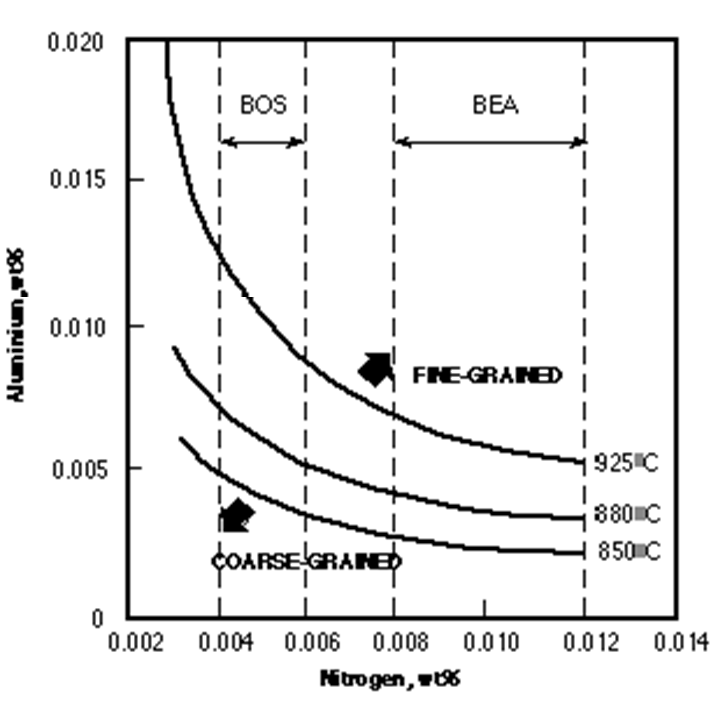
The effect of austenitisation temperature and nitrogen content on the tolerable aluminium in steel to avoid a grain size finer than ASTM 6. Based on an austenitisation time of 1 hour. Typical nitrogen levels in steels made via the two modern-day steelmaking routes, processing liquid iron (BOS) or recycling scrap (BEA), are superimposed on the diagram. Practical experience suggests that aluminium levels are generally at either the top (in excess of 0.020%) or the bottom (less than 0.005%) of the range shown.
Subject to the limitations listed below, it should be possible to use the diagram as a rough guide in assessing a steel’s suitability for hardening (i.e. whether it is likely to be fine-grained, and therefore potentially problematical, in heat treatment).
Limitations
- The full analysis of the steel in question must be known. Information on the content of aluminium, nitrogen and residual elements can be provided by reputable suppliers, although these elements are not yet reported as standard.
- The theoretical diagram sets the borderline between coarse and fine grain size between ASTM 6 and 7. In practice, most materials with a grain size coarser than ASTM 6 will heat treat without difficulty.
- The diagram is based on one hour at austenitisation temperature. The tolerable aluminium level would be lower for shorter times.
- The thermomechanical history of the steel prior to the heat treatment stage can have a bearing on the grain size developed.
Other considerations
Residual elements in plain-carbon steel can have a positive effect on hardenability and counter the negative aluminium-related influence. Their relative significance can be judged by their contribution to increasing ideal diameter, DI , as expressed(9) in inches (for steel with ≤ 0.40%C, ≤ 1.20%Mn and a grain size of ASTM 7) by:
DI = f(C) x f(Si) x f(Mn) x f(Cr) x f(Mo) x f(Ni) x f(Cu) x f(V)
where:
f(C) = 0.54 x %C
f(Si) = (0.7 x %Si) + 1
f(Mn) = (3.3333 x %Mn) + 1 f(Cr) = (2.16 x %Cr) + 1
f(Mo) = (3.0 x %Mo) + 1
f(Ni) = (0.363 x %Ni) +1
f(Cu) = (0.365 x %Cu) + 1
f(V) = (1.73 x %V) + 1
STEEL SELECTION
The foregoing underlines the care that must be applied when selecting a plain-carbon steel for components which will be case-hardened or straight hardened. As pointed out in the original joint statement(1-7), steelmakers can supply steels specifically suitable for hardening. The onus is on the specifier to ensure that his steel supplier is aware of all of his requirements, including reliable response to the heat treatment process he intends to select.
REFERENCES
- A JOINT STATEMENT BY THE STEEL INDUSTRY AND CHTA. HEAT TREATMENT OF METALS. 1994.1,VOL.21,7.
- A MESSAGE TO STEEL SUPPLIERS, STOCKHOLDERS, SPECIFIERS, USERS AND HEAT TREATERS. MATERIALS WORLD. MAR.1994, VOL.2,NO.3,148
- ALUMINIUM-CONTAINING PLAIN-CARBON STEELS – TECHNICAL ASPECTS ELABORATED.METALLURGIA.MAR.1994,VOL.61, NO.3, 78.
- HARDENABILITY FALLS IN AL-KILLED C STEELS. STEEL TIMES. MAR.1994.
- ALUMINIUM-CONTAINING PLAIN-CARBON STEELS. HOTLINE. APR.1994,NO.58,3.
- THE HEAT-TREATMENT RESPONSE OF ALUMINIUM-CONTAIN- ING STEELS. HOTLINE. JULY 1994,NO.59, INSERT.
- HEAT TREATMENT OF PLAIN CARBON STEELS CONTAINING ALUMINIUM. NASS NEWS. JUNE 1994,ISSUE 4,7.
- GLADMAN T. ALUMINIUM FOR GRAIN SIZE CONTROL. HEAT TREATMENT OF METALS. 1994.1, VOL.21,11-14.
- STANDARD METHOD OF END-QUENCH TEST FOR HARDENABILITY OF STEEL. ASTM A255, 1989.
This datasheet is compiled in good faith solely to assist others to evaluate the heat treatment techniques described. Users do so entirely at their own risk. NHTC is not responsible for any consequences from any such use. Datasheets shall not be used for contractual purposes neither directly nor by implication.