Data Centre
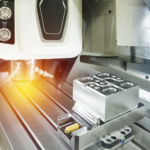
HARDENING AND TEMPERING OF TOOL AND DIE STEELS
Hardening involves controlled heating to a critical temperature dictated by the type of steel (in the range 760- 1300°C) followed by controlled cooling. Dependent on the type of material, appropriate cooling rates vary from very fast (water quench) to very slow (air cool). Tempering involves reheating the hardened tool/die to a temperature between 150-675°C, depending on the steel type. A process which controls final properties whilst relieving stresses after hardening, tempering can be com- plex; some steels must be subjected to multiple tempering operations.
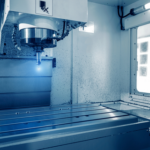
NITRIDING AND NITROCARBURISING
Gaseous Nitriding is conducted in gas (490-560°C) for treatment times ranging up to 90 hours and involves the diffusion of nitrogen into the surface to produce a controlled depth of hard alloy-nitrides. Unlike the high-temperature case-hardening treatments (carburizing / carbonitriding), hardening is achieved without the need for quenching. Nitrocarburising is generally of shorter duration (30 minutes - 5 hours), involves enrichment of the surface with both nitrogen and carbon to impart a thin iron-carbonitride “compound layer” supported by a nitrogen-bearing “diffusion zone” and conducted at temperatures of 560-580°C.
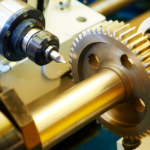
ANTICIPATING THE HARDENING RESPONSE OF ALUMINIUM-BEARING PLAIN-CARBON STEELS
Addressed the unexpectedly poor response (low hardness and/or case depth), of a steel containing significant levels of aluminium, after heat treatment under normal conditions which would otherwise be expected to yield satisfactory results.
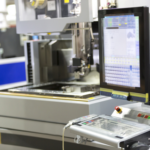
CARBURISING AND CARBONITRIDING (CASE HARDENING)
Carburising and carbonitriding are “thermochemical” treatments, usually conducted at temperatures in the range 800-940°C, in the first stage of “case-hardening”. These processes change the chemical composition of the surface of a low-carbon steel component so that subsequent fast cooling, by “quenching”, produces a hard “case” combined with a softer/tougher “core”. Quenching is normally followed by a low-temperature tempering / stress relieving treatment.
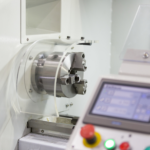
INDUCTION HARDENING
Induction hardening is a method for hardening the surfaces of components, usually in selected areas, by the short-time application of high-intensity heating followed by quenching. The heating and hardening effects are localised and the depth of hardening is controllable. Unlike thermochemical case-hardening treatments (carburising / carbonitriding) applied to low-carbon steels, induction hardening does not promote chemical enrichment of the surface with carbon, but rely on the presence of an adequate carbon content already in the material to achieve the hardness level required.
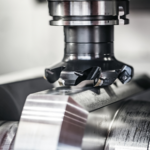
STRESS RELIEVING, NORMALISING AND ANNEALING
Stress relieving is applied to both ferrous and non-ferrous alloys and is intended to remove internal residual stresses generated by prior manufacturing processes such as machining, cold rolling and welding. Normalising is applied to some, but not all, engineering steels, normalising can soften, harden or stress relieve a material, depending on its initial state. The objective of the treatment is to counter the effects of prior processes, such as casting, forging or rolling, by refining the existing non-uniform structure into one which enhances machinability/formability or, in certain product forms, meets final mechanical property requirements. The primary purpose of an annealing treatment is to reduce the hardness of a material and facilitate the progress of subsequent manufacturing operations.